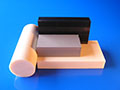
TridentShapes™ ABS
TridentShapes™ ABS is an excellent choice for applications which require high impact resistance, strength and stiffness. Trident ABS is an ideal material for machining structural components and pre-production prototypes. ABS resin is a terpolymer formed by blending an amorphous thermoplastic copolymer of acrylonitrile and styrene with an elastomeric component, such as polybutadiene or a butadiene polymer. By altering the ratio of these three monomers, ABS resins can offer an expansive assortment of performance properties tailored to meet a wide range of end-use requirements. Because of its good balance of properties, toughness-strength-temperature resistance coupled with its ease of processing, TridentShapes™ ABS has a very wide range of applications.
Characteristics
• Lightweight
• Easy to fabricate
• Good strength & stiffness
• High impact resistance
• Excellent aesthetic properties
Applications
• Structural components
• Housings
• Support blocks
• Models
• Machined prototypes
Annealed Plate: .250 through 6.00" thick
Plate sizes: 24x48 • 48x96 • 50x124 • 30x60
Extruded Rod: .250 through 8.00" diameter
Cut to size shapes and custom sizes available on request
Tubular bar: up to 8.00" diameter, wall sizes up to .500"
Agency ratings: FDA 21CFR 181.32 • ASTM D4673 ABS0110 B54240
Physical | Nominal Value | Unit | Nominal Value | Unit | Test Method | ||||
Density / Specific Gravity | 0.037 | lb/in3 | 1.040 | g/cm3 | ASTM D1505 | ||||
Mechanical | Nominal Value | Unit | Nominal Value | Unit | Test Method | ||||
Tensile Modulus | 329000 | psi | 2270 | Mpa | ASTM D638 | ||||
Tensile Strength (Yield) | 6380 | psi | 44 | Mpa | ASTM D638 | ||||
Tensile Strength (Break) | 4790 | psi | 33 | Mpa | ASTM D638 | ||||
Tensile Elongation (Yield) | 2 | % | 2 | % | ASTM D638 | ||||
Tensile Elongation (Break) | 24 | % | 24 | % | ASTM D638 | ||||
Flexural Modulus | 334000 | psi | 2305 | Mpa | ASTM D790 | ||||
Flexural Strength | 10200 | psi | 70 | Mpa | ASTM D790 | ||||
Impact | Nominal Value | Unit | Nominal Value | Unit | Test Method | ||||
Notched Izod Impact 73ºF (23ºC) | 6 | ft-lb/inch | 320 | J/m | ASTM D256 | ||||
Instrumented Dart Impact 73ºF (23ºC) Total Energy | 266 | in-lb | 30 | J | ASTM D3763 | ||||
Hardness | Nominal Value | Unit | Nominal Value | Unit | Test Method | ||||
Rockwell Hardness | 112 | R scale | 112 | R scale | ASTM D785 | ||||
Thermal | Nominal Value | Unit | Nominal Value | Unit | Test Method | ||||
Deflection Temperature 66 psi | 201 | ºF | 93.96 | ºC | ASTM D648 | ||||
Deflection Temperature 264 psi | 176 | ºF | 80.06 | ºC | ASTM D648 | ||||
Vicat Softening Temperature | 210 | ºF | 98.97 | ºC | ASTM D15252 | ||||
Electrical | Nominal Value | Unit | Nominal Value | Unit | Test Method | ||||
Arc Resistance | PLC 6 | PLC 6 | ASTM D495 | ||||||
Comparative Tracking Index (CTI) | PLC 0 | PLC 0 | UL 746A | ||||||
High Amp Arc Ignition (HAI) | PLC 0 | PLC 0 | UL 746A | ||||||
High Voltage Arc Resistance to Ignition (HVAR) | PLC 3 | PLC 3 | UL 746A | ||||||
Hot-wire Ignition (HWI) | PLC 3 | PLC 3 | UL 746A | ||||||
Flammability | Nominal Value | Unit | Nominal Value | Unit | Test Method | ||||
Flammability Rating | HB @ .059 | HB @ 1.5mm | UL94 | ||||||
* This information is based on average resin value specifications and is only to assist and advise you on the current technical knowledge, it is given without obligations or liability. |
/Asset/ABS_shapes.jpg
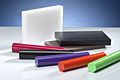
Acetal POM Shapes
Acetal polymers, referred to chemically as POM PolyOxyMethylene, are semi-crystalline
engineering thermoplastics made by the polymerization of formaldehyde. They have
physical properties that are not available with metals or most other plastics; high
mechanical strength and rigidity, low coefficients of friction, low moisture absorption,
excellent dimensional stability, fatigue endurance, and resistance to abrasion and
creep. These materials are also resistant to a wide range of solvents and have good
electrical properties.
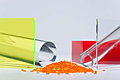
Acrylic - PMMA
Acrylic (PMMA) materials have an unusual combination of properties, outstanding weather resistance, brilliant clarity, "light-piping" and "edge-lighting" qualities, chemical resistance, and ease of forming and machining. Compared to all other types of transparent thermoplastics, acrylic has outstanding resistance to the damaging effects of sunlight and outdoor weathering. Acrylic is often recognized under brand names such as Acrylite®, Plexiglas®, Lucite®, Optix®, Polycast®, Perspex® and Chemcast®.
/Asset/Acrylite3.jpg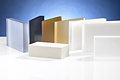
Halar® ECTFE
Halar® ECTFE is a partially fluorinated semi-crystalline polymer offering a unique combination of mechanical properties, thermal and chemical resistance with an outstanding ease of processability. Halar ECTFE, a copolymer of ethylene and chlorotrifluoroethylene, can bring advantages to the end user when compared to other fluoropolymers. It is a very versatile polymer, available in all forms to meet processing needs. Halar offers excellent resistance to abrasion, harsh chemicals, and permeation. Halar® is a registered trademark of Solvay. /Asset/Misc Materials1.jpg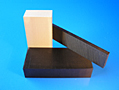
NORYL® PPO
Typical characteristics of NORYL® include excellent dimensional stability, low mold shrinkage, low water absorption and very low creep behavior at elevated temperatures. These properties combined with an outstanding hydrolytic stability in hot and cold water, make NORYL® an excellent potential candidate for fluid engineering applications.Another outstanding feature of NORYL® is its retention of tensile and flexural strength, even at elevated temperatures. The gradual reduction in modulus as temperature is increased, is a key advantage of this material. As a result, parts fabricated from NORYL® shapes may be used with predictable performance over a wide temperature range. Another important advantage of NORYL® is its predictably low creep behavior, even at elevated temperatures.
NORYL® exhibits excellent electrical properties, which remain stable over a wide range of temperature, humidity and frequency variations. This stability, together with a fine-tuned balance of thermal and impact properties, makes NORYL® an excellent potential candidate for demanding electrical and electronic applications, including electrical insulators.
All flame retardant NORYL® resins are designed with non-brominated and non-chlorinated flame retardant systems. /Asset/NORYL.jpg
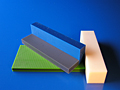
Nylon - Cast
Cast Nylons are a range of polyamides produced by a casting process involving the anionic polymerisation of caprolactum. This process allows the production of semi-finished plate, rod, tube and custom castings that are largely free of internal stresses. Natural Cast Nylon is the basic grade from which all other grades of Cast Nylons stem. Generally accepted as the primary engineering polymer, Natural Cast Nylon is suitable for virtually any plain bearing application not to mention a huge range of other applications for which this versatile grade finds a use. By varying the conditions of polymerisation the mechanical properties of Cast Nylon may be altered to suit specific applications and the addition of various additives, fillers, lubricants and colorants.- Natural Un-filled.
- Blue Heat Stabilized.
- Black
- MDS (MoS2) Molybdenum disulfide-filled
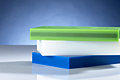
Nylon - Extruded
Nylon’s toughness, low coefficient of friction and good abrasion resistance make it an ideal replacement for a wide variety of materials from metal to rubber. It weighs on 1/7 as much as bronze. Using nylon reduces lubrication requirements, eliminates galling, corrosion and pilferage problems, and improves wear resistance and sound dampening characteristics. Nylon has a proven record of outstanding service in a multitude of parts for such diverse fields as paper, textiles, electronics, construction, mining metalworking, aircraft, food and material handling. Nylon is easily fabricated into precision parts using standard metalworking equipment. /Asset/Nylon PA66.jpg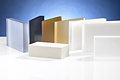
PCTFE
PCTFE (KEL-F®)/Poly-Chloro-Tri-Fluoro-Ethylene is a fluorocarbon based polymer and is commonly abbreviated PCTFE. The KEL-F® brand is a registered trademark of the 3M Corporation, but was discontinued in 1995. The only remaining brand, NEOFLON® is made by Daikin Industries of Japan. This PCTFE has the same chemical structure and properties as the original KEL-F® brand PCTFE. PCTFE offers the unique combination of physical and mechanical properties, non-flammability, chemical resistance, near zero moisture absorption, and excellent electrical properties. These characteristics cannot be found in any other thermoplastic fluoropolymer with a useful temperature range of -400°F to +300°F. PCTFE also has extremely low outgassing (0.01% TML, 0.00% WVR when tested per ASTM E595-90), so it is suitable for use in aerospace and flight applications. /Asset/Misc Materials1.jpg
PEEK
PEEK is a unique semi-crystalline, high temperature engineering thermoplastic, is an excellent material for a wide spectrum of applications where thermal, chemical, and combustion properties are critical to performance. Especially significant, in this regard, is PEEK's ability to retain its flexural and tensile properties at very high temperatures–in excess of 482°F. /Asset/PEEK PARTS1.jpg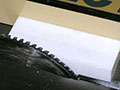
PET / Ertalyte®
PET is an unreinforced, semi-crystalline thermoplastic polyester based on polyethylene terephthalate (PET). It is characterized as having the best dimensional stability coupled with excellent wear resistance, a low coefficient of friction, high strength, and resistance to moderately acidic solutions. PET's properties make it especially suitable for the manufacture of precision mechanical parts which are capable of sustaining high loads and enduring wear conditions. PET's continuous service temperature is 210°F and its melting point is almost 150° F higher than Acetal. It retains significantly more of its original strength up to 180°F than Nylon or Acetal. In addition, PET offers good chemical and abrasion resistance. Its low moisture absorption enables mechanical and electrical properties to remain virtually unaffected by moisture. PET can be machined to precise detail on standard metal working equipment. /Asset/PET_1.jpg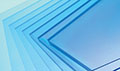
PETG / Vivak®
PETG is a transparent, thermoplastic sheet used widely in the point of purchase industry. PETG products offer superior impact strength over acrylic and cost effectiveness compared to polycarbonate, and offers deep draws, complex die-cuts, and precise molded-in details without sacrificing structural integrity. It die-cuts and punches easily, and can be bonded or fastened with adhesives, ultrasonic welding, or rivets. In addition, PETG is easily decorated by painting, silk screening, or hot stamping. Easy to fabricate, form, bond, and decorate, PETG sheet products are well suited for a variety of point of purchase and other applications. /Asset/PETG1.jpg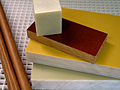
Thermoset Composite
Thermoset composite industrial laminates are made by applying heat and pressure to layers of paper, canvas, linen or glass cloth impregnated with synthetic themosetting resins. When heat and pressure are applied to the layers, a chemical reaction (polymerization) transforms the separate layers into a single laminated material with a "set" shape that cannot be softened again - therefore, these materials are called "thermosets". A variety of resin types and cloth materials can be used to manufacture thermoset composite laminates with a range of mechanical, thermal, and electrical properties. Physical strength, resiliency, ease and versatility of fabrication, and excellent electrical properties make these laminates useful as support components in a wide range of mechanical and electrical applications. Thermoset Composite Laminates are strong, stiff, and have high impact and compressive strengths. And they do not soften upon re-heating, so they are easy to saw, drill, tap, and machine with ordinary tools. Mechanical and Electrical grades are available which are excellent choices for intricate punch parts, insulating washers, spacers, terminal boards, switch bases, and other electrical components. /Asset/Glass Laminate.jpg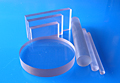
Polycarbonate
Polycarbonate is an amorphous engineering thermoplastic, which is charactarized by high levels of mechanical, optical, electrical and thermal properties. Polycarbonate is one of the most widely used engineering materials in the world and has contributed to product revolutions in virtually every industry. Polycarbonate shapes have outstanding impact strength, superior dimensional stability, high temperature resistance and high clarity.
/Asset/PC14.jpg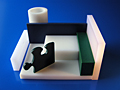
Polyethylene
Polyethylene or polyethene is a thermoplastic commodity heavily used in consumer products (over 60M tons are produced worldwide every year). Its name originates from the monomer ethene, also known as ethylene, used to create the polymer. Polyethylene stock shapes are classified into three categories [LDPE, HDPE & UHMW-PE] based mostly on its density and branching. The mechanical properties of PE depend significantly on variables such as the extent and type of branching, the crystal structure, and the molecular weight. /Asset/PE2.jpg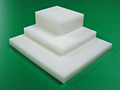
Polypropylene
Polypropylene is an economical material that offers a combination of outstanding physical, chemical, mechanical, thermal and electrical properties not found in any other thermoplastic. Compared to low or high density polyethylene, it has a lower impact strength, but superior working temperature and tensile strength. Polypropylene provides excellent resistance to organic solvents, degreasing agents and electrolytic attack. It is lightweight, resistant to staining, and has a low moisture absorption rate. This is a tough, heat-resistant, semi-rigid material, ideal for the transfer of hot liquids or gases. It is recommended for vacuum systems and where higher heats and pressures are encountered. It has excellent resistance to acids and alkalines, but poor resistance to aromatic, aliphatic and chlorinated solvents. /Asset/PE1.jpg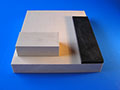
PPS - PolyphenyleneSulfide
PPS (polyphenylene sulfide) products offer the broadest resistance to chemicals of any advanced engineering plastic. They have no known solvents below 392°F and offer inertness to steam, strong bases, fuels and acids. Minimal moisture absorption and a very low coefficient of linear thermal expansion, combined with a proprietary stress relieving processes, make PPS shapes ideally suited for precise tolerance machined components. In addition, PPS products exhibit excellent electrical characteristics and are inherently flame retardant. /Asset/PPS11.jpg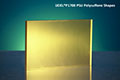
PSU Polysulfone
UDEL® P-1700 Natural Polysulfone (PSU) is a semi-transparent (Amber color), heat resistant, high performance engineering thermoplastic. It offers excellent mechanical, electrical and improved chemical resistance properties relative to polycarbonate. Polysulfone’s properties remain relatively consistent over a broad temperature range, from –150°F (–100°C) to 300°F (100°C). UDEL® Polysulfone is hydrolysis resistant for continuous use in hot water and steam at temperatures up to 300°F. Its flame resistance is UL94 V0 at .177” thickness (4.5mm). UDEL® Polysulfone offers high chemical resistance to acidic and salt solutions, and good resistance to detergents, hot water and steam. In addition, polysulfone is highly resistant to degradation by gamma or electron beam radiation, and offers low ionic impurity levels. Electrical properties of UDEL Polysulfones are stable over a wide temperature range and after immersion in water or exposure to high humidity. UDEL® Polysulfone often replaces polycarbonate when higher temperatures, improved chemical resistance or autoclavability is required. It is commonly used for analytical instrumentation, medical devices and semiconductor process equipment components. Contact customer service for a complete list of physical, mechanical, thermal and electrical properties. /Asset/4PSU.jpg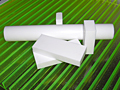
PTFE / Teflon®
TEFLON® PTFE / Polytetrafluoroethylene is a completely fluorinated polymer manufactured by free radical polymerization of tetrafluoroethylene. PTFE is a crystalline polymer with a melting point of about 621°F. Density is 2.13 to 2.19 g. PTFE has exceptional resistance to chemicals. Its dielectric constant (2.1) and loss factor are low and stable across wide temperature and frequency range. PTFE has useful mechanical properties from cryogenic temperatures, up to 500°F. Its coefficient of friction is lower than almost any other material. One of the most versatile plastic materials known, PTFE is useful for a large range of products for applications excluded to other materials. /Asset/PTFE2.jpg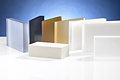
Radel® PPSU Polyphenylsulfone
Radel®R is a Polyphenylsulfone (PPSU) suited primarily to applications in the medical industry. Radel®R is similar to Polysulfone (PSU) but has improved performance in terms of temperature, impact strength and chemical resistance. Radel®R also has exceptional resistance to repeated steam autoclaving without loss of dimensional stability or physical properties.
/Asset/Misc Materials1.jpg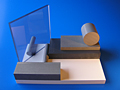
PVC
Polyvinyl Chloride / PVC or Vinyl is usually an amorphous thermoplastic material with excellent chemical resistance and dielectric properties, good tensile, flexural and mechanical strength, low moisture absorption, exceptional dimensional stability and good flammability characteristics. The maximum service temperature for PVC is 140°F. The physical properties of PVC can be readily altered by the addition of plasticizers, impact modifiers and other ingredients to develop and enhance specific properties. Generally, there are two basic types of PVC available - Rigid PVC and Flexible (plasticized) PVC. Fabricated by hot gas welding, fusion, butt welding, ultrasonic sealing, die cutting, vacuum forming and thermoforming, and standard machining techniques. /Asset/PVC1.jpg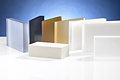
PVDF - Kynar®
Kynar® PVDF Polyvinyldenefluoride offers excellent corrosion and chemical resistance at both ambient and elevated temperatures (up to 280°F). PVDF is also inherently UV stable, mechanically tough, abrasion and flame resistant. Kynar® PVDF are highly chemically resistant fluoropolymers used in piping, tubing, vessel fabrication, machined valves and fittings, nozzles and other items for corrosive fluid handling. Their inherent chemical resistance and high purity make them ideal for application in contact with high purity water, acids, chlorine, halogenated solvents and petrochemical mixtures. /Asset/Misc Materials1.jpg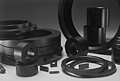
Torlon® PAI - Polyamide-imide
Torlon is the one of the highest performing, melt processable plastics available. It has superior resistance to elevated temperatures. It is capable of performing under severe stress conditions at continuous temperatures to 500°F (260°C). Parts machined from Torlon stock shapes provide greater compressive strength and higher impact resistance than most advanced engineering plastics. Torlon PAI’s extremely low coefficient of linear thermal expansion and high creep resistance deliver excellent dimensional stability over its entire service range. Torlon is an amorphous material with a Tg (glass transition temperature) of 537°F (280°C).
/Asset/TORLON11.jpg